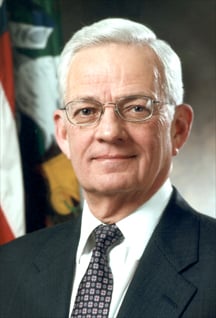
A great safety speech isn't about telling staff to improve safety. Instead, it's a unique opportunity to motivate staff to work together for a common good.
On a windy...
Back in 1987, every Alcoa plant, worldwide, had at least one accident per week. It was dangerous work. Molten metals bubbled at 1,500 degrees and machines that could literally rip off a man's arm were used every day. It was commonly accepted that some staff wouldn't make it home.
Yet, within a relatively short time, Alcoa became one of the safest companies to work at. Rather astonishingly, the worker injury rate dropped to one-twentieth of the US average. To this day, Alcoa is still exemplary when it comes to safety. In fact, the injury rate continues to decrease. It is now safer to work at Alcoa than a working at a movie studio, software company or accountancy firm.
So what happened? What changed Alcoa?
Safety and Paul O'Neill
According to The Power of Habit by Charles Duhigg, Paul O'Neill the then newly knighted CEO of Alcoa, managed to improve not only safety, but company profitability all at the same time. By focusing on improving workplace habits, O'Neill turned Alcoa around, in a way no-one thought possible.
It all started in October 1987, when he made the rather surprising move for a CEO when at his maiden company speech, he chose a shareholder meeting to announce his focus on worker safety (and not the commonly expected CEO focus on making money). His speech is arguably the best safety speech of all time (which you can read at Is this the best CEO safety speech ever?).
At the time, Alcoa was in a mess. The unions were unhappy and so were thousands of workers who regularly went on strike. The company had been steadily losing money year after year with failed product lines, poor safety and productivity.
O'Neill, a former high ranking Government official believed that he needed to focus on what would bring Alcoa together - including unions and executives. And who could argue with him? Unions had been complaining about safety for ages, while managers knew poor safety contributed to low morale and lost productivity. He also knew that he had to change their routines. In his inaugural speech he said: "If we bring our injury rates down, it won't be because of cheer-leading or the nonsense you sometimes hear from CEOs. It will be because the individuals at this company have agreed to be part of something important. They've devoted themselves to creating a habit of excellence. Safety will be an indicator that we're making progress in changing our habits across the entire institution That's how we should be judged".
Changing Safety Habits
While unions, Wall Street and senior executives who were passed over for promotion panicked about what O'Neill was planning to do, he set to work. He improved Alcoa by focusing on four core areas:
1. Work out Why
In the book, Start with a Why, by Simon Sinek he mentions that mediocre companies when they start any initiative, be that marketing or a business process, first focus on the what and how and then why last. Yet, when companies first question why, the company does what it does, they often uncover hidden truths that enables everyone to truly understand what to do.
To reach zero injuries, O'Neill started to investigate why injuries were happening in the first place. To do this, Alcoa had to study how things were going wrong in the manufacturing process. Once that was worked out, people were brought in to retrain staff on more efficient and safer work processes.
The result was the Alcoa became more streamlined and productive. After all, correct work is safer work.
2. Change Routines
In the book, The Power of Habit by Charles Duhigg, he explains the importance of the habit loop to change individual or even group behaviour.
Essentially, all habits include three steps. Let's take a look at how the regular habit of cleaning your teeth works:
All three steps need a firm belief that you are able to clean your teeth. This ensures you stick with your habit when life gets challenging.
Intuitively, O'Neill changed safety behaviours by using the same habit loop:
Staff quickly learnt that if they wanted to get promoted, they had to start reporting and solving injuries. Meanwhile, O'Neill made sure that everyone believed that Alcoa could be a safe place to work.
3. Improve Communication
To improve workplace safety behaviours, it also meant that communication had to be overhauled in many different ways.
Vice Presidents had to start regularly communicating with floor managers, who in turn had to be in regular communication with the frontline workers. While frontline workers had to constantly think about safety improvements because they knew if an injury was reported, they would need to give the floor manager a plan, so that the Vice President had a plan to present to O'Neill.
Rather surprisingly, O'Neill gave out his personal phone number to everyone and stressed that if management was not following up on safety, that people could call him at home. He also gave frequent speeches and wrote regular communication pieces to staff about progress.
Previously, Alcoa had a rigid silo mentality which had thrived on departments working separately and not communicating with each other. Under the new system, silos broke down. Even the hierarchy crumbled, as now it was necessary for clear communication, and solutions between all levels.
In fact, so important was the need for Alcoa workers to communicate about safety at their own site, but also Alcoa sites across the world, that O'Neill took the unprecedented step of ordering Alcoa's worldwide offices to link up to an electronic network.
Alcoa had one of the first genuinely worldwide corporate email systems developed in the late 1980's, allowing staff to see safety data, in real time, around the world.
Amazingly, the opening of communication across Alcoa improved the company in more ways than just safety.
Frontline workers began to feel confident that they could suggest ideas to improve production. even if that meant phoning O'Neill at home with improvements. One such worker had an innovative idea to improve how Alcoa grouped painting machines together, which meant they could switch out pigments faster and become quicker at responding to changing demands in customer colours. This suggestion alone doubled profits on aluminium sidings in one year. Frustratingly, the same worker had been suggesting the improvement for 10 years to deaf ears.
4. Small Wins
The academic Geoffrey Hodgson wrote that "Individuals have habits; groups have routines. Routines are the organisational analogue of habits".
To change habits effectively, and to get momentum going, Alcoa had to experience some "small wins". Unfortunately, to get to this point, pain was experienced.
Six months after implementing the new safety habits, a tragedy struck Alcoa. A new worker that was young and keen was killed instantly when he unjammed an extrusion press.
O'Neill received the gruesome news at night and within 14 hours he was at an emergency meeting in Pittsburgh with all of the plant's executives and officers to painstakingly run through the accident and work out what went wrong. They discovered dozens of mistakes that had been responsible for the death. From those mistakes they implemented new procedures such as ensuring that during training, workers knew they wouldn't be blamed for equipment breakdowns and that managers did not allow anyone to jump over barriers.
A week later, all safety railings at Alcoa's plants were painted yellow, new policies were written and managers asked employees to suggest proactive maintenance ideas and rules were updated to specify that no one would attempt unsafe repairs.
And then finally, Alcoa experienced a small win. A considerable decline in the injury worker rate.
The unfortunate death acted as a tipping point that increased staff motivation to change safety habits. It brought about such a profound shift with safety habits that the change inevitably spilled over into other parts of worker lives. New ideas were regularly suggested, productivity surged and staff leveraged the new email system, to not just communicate safety, but to give Alcoa the edge in sending pricing intelligence to their other international sites. It was like a secret weapon that took years for the competition to figure out.
Keystone Habits
With any new safety plan or initiative, changing key safety habits and routines is critical for success.
Interestingly, as Charles Duhigg writes in The Power of Habit, when people start changing their habits, they start changing other unrelated patterns in their lives, often unwittingly. Research has found that families who eat dinner every night together have children with better homework skills, greater emotional control more confidence and better grades. While those who start exercising regularly. start to eat better and become more productive at work.
Known as keystone habits, some habits are more important than others because they have the power to start a chain reaction, shifting other patterns as they move through our lives. Keystone habits influence how we work, eat, play, live, spend, and communicate. Keystone habits start a process that, over time, transforms everything.
To improve safety at Alcoa, O'Neill had to totally transform corporate habits. While he never promised improved profits, the company became more profitable. As safety improved, costs decreased. Raw materials were no longer spilled so frequently, broken down equipment was replaced which resulted in higher quality products being manufactured, as equipment malfunctions affected product quality detrimentally.
Being fixated on improving company safety enabled Alcoa to improve company productivity and profitability in ways unfathomable to the average business leader.
Is this a safety plan your company could implement?
A great safety speech isn't about telling staff to improve safety. Instead, it's a unique opportunity to motivate staff to work together for a common good.
On a windy...
In a wood-panelled conference room in Seattle, a handsome dark-haired man called Nick sits with three people. They are all working together on a marketing plan for a...