As a safety content producer, I get the rare chance to look at countless standard operating procedures from a variety of large companies.
We use these documents to write clear, friendly scripts, in order to produce training videos that will engage, increase learner understanding and recall. Nearly, 95% of the time, these standard operating procedures are really hard to read and understand. And they're very often wrong.
Yes, so wrong, that when we go out to film and we direct our helper for the day to undertake the procedure we get "We don't do that here. We do this."
This means that we have to make changes to the script on the spot and spend a bit of time discovering the actual process and whether it is the right way to do it. This means a bit of consulting with the OHS manager, before we can get back to the art of filming. In the edit suite, it also means we spend more time on that section getting it right because it's a procedure that no-one has much clarity on, so it's important we make it really clear, even if we don't always have the right information.
Here is a list of five of the top mistakes we find time and time again in standard operating procedures (or SOP's):
- Head office or Committees write the documents - if ever there was a bad way to write documents, it's like this. Usually the procedures are written in corporate speak with big words and long sentences. It's always about "persons" and what they can and can't do. Using a language that no-one would speak out on the floor (or in an office, unless they are an uptight lawyer with no friends). They read like legal documents where the focus is on protecting the company (and those who wrote it) and little effort is made to help staff members understand what to do correctly (I could go on for days about this, as it's a pet hate of mine). Often, the procedures are incorrect and head office or committees don't know how to improve them nor do they have the time to care.
- Supervisors and other staff members write the documents - This is a better option than head office or committees because they should know what they're writing about. Sort of. But then usually because they don't feel comfortable writing, they write to impress their high school teacher. So again, out come the big words and long sentences. But because one site often does processes in a different way, you often get procedures that are irrelevant for different sites. This results in standard operating procedures that are not necessarily based on best practice. Generally, these SOP's get ignored because procedures are incorrect and inconsistent for a particular site.
- Pass on the how but forget the why - A lot of SOPs pass on the 'how', but not the 'why.' This means that company processes get repeated without people ever questioning why they need to do something. Over time, staff are taught processes that solve problems that no longer exist. Empower your staff by explaining why they have to something, so they know whether that process is redundant when things change. Read more about this in "The Importance of Why in Workplace Training".
- Boring formatting and lots of text - Educational researchers have found that 83% of human learning occurs visually. We all know how easy it is to learn from a picture than a page of poorly written or complicated text. Yet, probably less than 50% of the standard operating procedures I've had to trawl through have used any photos or diagrams.
- Negative, unfriendly writing style - Humans tend to ignore negative words such as "don't or "can't", instead hearing the word after. So if you say "Don't run" many will just hear run. Rather than tell people what you don't want them to do, say what you want. So say "Walk slowly" instead. Often, standard operating procedures are full of lots of negative language. In fact, I worked on one that was so negative it treated the reader like they were already disobedient and a little on the stupid side. It was very off-putting and if I was a new starter, I would have been making plans to look for a new job (interestingly, this company has low turnover and good levels of morale, it was just head office protecting themselves, while the individual sites must have been making new starters feel welcome, regardless of the training manuals).
Three Steps to Fixing Up your Standard Operating Procedures
The better types of standard operating procedures I've read have been written by training managers or really, really passionate OHS managers who are always trying to work out the best way to communicate training messages. But they usually have mistakes lurking somewhere - a few incorrect procedures or challenging language.
A great resource for improving safety training and information, can be found in the book, Transform Your Safety Communication. It even includes templates to make writing easier. Here are some of the tips that are recommened to improve your SOPs or even your induction and training manuals:
- Get an outsider to read your standard operating procedures. This is a great litmus test, as to how well a lay-person understands the information. Often, when you're an expert in your field you have "The Curse of Knowledge". This means the more you know in a certain field the harder it is to break the information down, so that a new person to the field can understand it. Either you give more information than a person needs to understand or too little. Give your SOPs to your kids, friends, family or external business colleagues to read. If it's written well, a child should be able to understand it.
- Ask Why - Go through every procedure and ask why do we do that? You'll be surprised about how much redundant information you have that can be deleted. I regularly do this with clients (yes, I ring people up and annoy them by asking "Why do you this?" and "Why do you do that?") and it's amazing to discover how much information I can delete.
- Go out and do the procedures according to the SOPs - This is a great way to test if they're still relevant and whether they make sense. Use this time to take clear photos, that you can add into your documents. Our clients get a lot of benefit from us querying why they do a procedure out in the field and getting the process documented and filmed correctly.
- Use marketing and communication techniques to really lift the readibility of your training information. Try different ideas and techniques. If marketers can sell boring products, then they have the techniques to "sell" a mundane process. A great resource is Transform Your Safety Communication, get a free chapter here.
Having consistent and up-to-date training materials is a legal requirement. Ensuring that your standard operating procedures are correct is important for business safety and productivity. Start improving your procedures now and ensure all staff are doing the right procedure every time, everywhere.
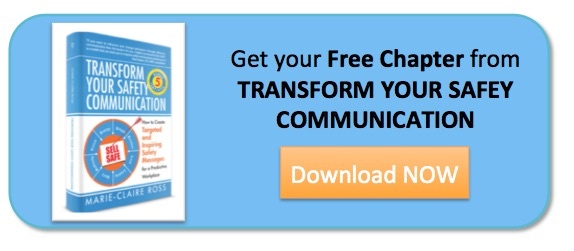